Sheet metal forming:
Sheet metal forming processes are those in which force is applied to a piece of sheet metal to modify its geometry rather than remove any material. The applied force stresses the metal beyond its yeild strength, causing the material to plastically deform, but not to fail. By doing so, the sheet can be bent or stretched into a variety of complex shapes. Sheet metal forming processes include the following:
Bending:
Bending is a metal forming process in which a force is applied to a piece of sheet metal, causing it to bend at an angle and form the desired shape. A bending operation causes deformation along one axis, but a sequence of several different operations can be performed to create a complex part. Bent parts can be quite small, such as a bracket, or up to 20 feet in length, such as a large enclosure or chassis. A bend can be characterized by several different parameters, shown in the image below.
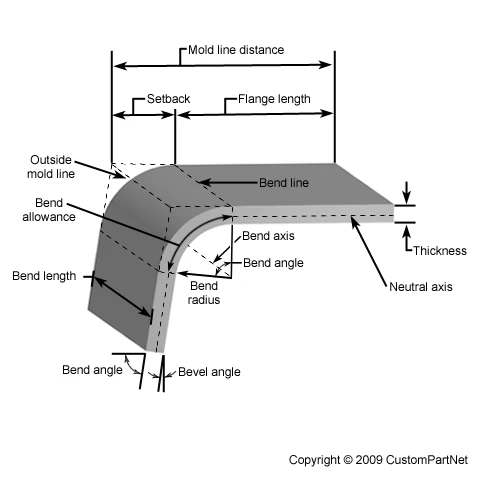
- Bend line - The straight line on the surface of the sheet, on either side of the bend, that defines the end of the level flange and the start of the bend.
- Outside mold line - The straight line where the outside surfaces of the two flanges would meet, were they to continue. This line defines the edge of a mold that would bound the bent sheet metal.
- Flange length - The length of either of the two flanges, extending from the edge of the sheet to the bend line.
- Mold line distance - The distance from either end of the sheet to the outside mold line.
- Setback - The distance from either bend line to the outside mold line. Also equal to the difference between the mold line distance and the flange length.
- Bend axis - The straight line that defines the center around which the sheet metal is bent.
- Bend length - The length of the bend, measured along the bend axis.
- Bend radius - The distance from the bend axis to the inside surface of the material, between the bend lines. Sometimes specified as the inside bend radius. The outside bend radius is equal to the inside bend radius plus the sheet thickness.
- Bend angle - The angle of the bend, measured between the bent flange and its original position, or as the included angle between perpendicular lines drawn from the bend lines.
- Bevel angle - The complimentary angle to the bend angle.
The act of bending results in both tension and compression in the sheet metal. The outside portion of the sheet will undergo tension and stretch to a greater length, while the inside portion experiences compression and shortens. The neutral axis is the boundary line inside the sheet metal, along which no tension or compression forces are present. As a result, the length of this axis remains constant. The changes in length to the outside and inside surfaces can be related to the original flat length by two parameters, the bend allowance and bend deduction, which are defined below.
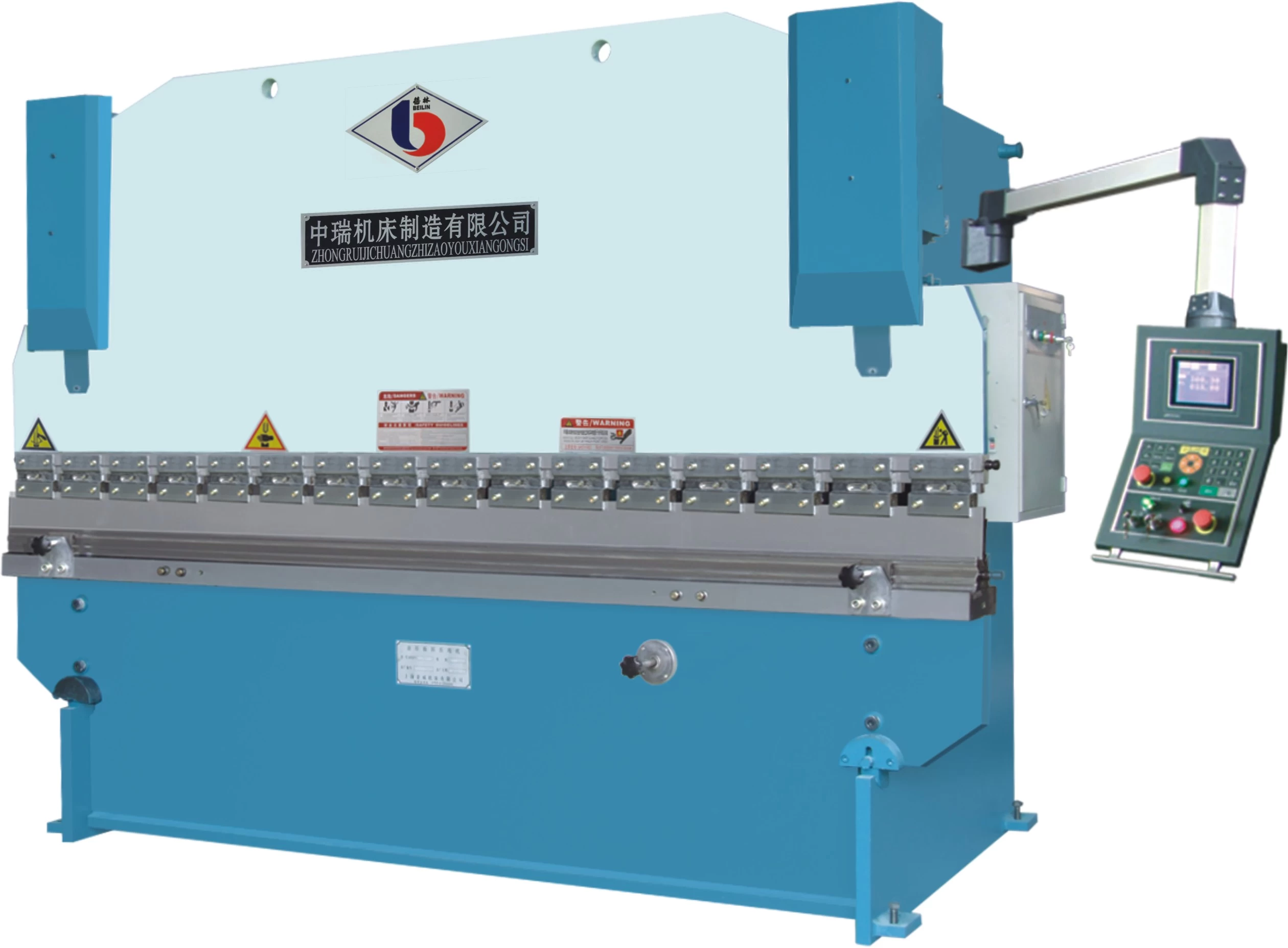
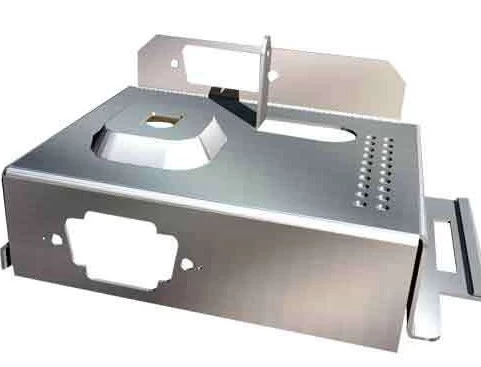
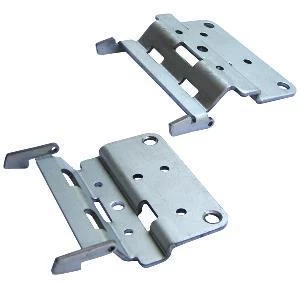